COMPANY
50 YEARS OF NYLON 6 & 66 PRODUCTION
NUREL fibers
NUREL started its operations producing polyamide fiber in 1968 and i was acquired by SAMCA Group. The entrance of SAMCA Group in 1999 brought successive investments in new polymerization and spinning technologies. Thanks to this and to the security of belonging to a solid industrial group, NUREL has become a global reference supplier of nylon 6 and 66.
LEADING EUROPEAN TEXTILE INNOVATION
At NUREL we currently havetwo cutting-edge nylon spinning plants and outstanding draw-warping facilities that enable us to offer a range of products for lingerie, swimwear, sports and various technical applications which are unique in the market and able to meet most demanding customer’s expectations.
A continuous investment on R&D and state-of-the-art technologies demonstrates our deep commitment towards the future of the textile industry; our innovation efforts are focussed on new technologies such as nanotechnology, smart textiles and other different programs of functional textiles.
LOCAL PRODUCTION, GLOBAL PRESENCE
NUREL has three differentiated business units: ENGINEERING POLYMERS, BIOPOLYMERS and SYNTHETIC FIBERS. Over the years NUREL has achieved an overall turnover of 80 Million Euros, with a polymer capacity of 27,000 tons, and 7,500 tons of yarn production. Oursite in Zaragoza employs overall 350 people. Approximately 70% of our fibers production is sold abroad to the main European and Asiatic markets.
NUREL started its operations producing polyamide fiber in 1968 and i was acquired by SAMCA Group. The entrance of SAMCA Group in 1999 brought successive investments in new polymerization and spinning technologies. Thanks to this and to the security of belonging to a solid industrial group, NUREL has become a global reference supplier of nylon 6 and 66.
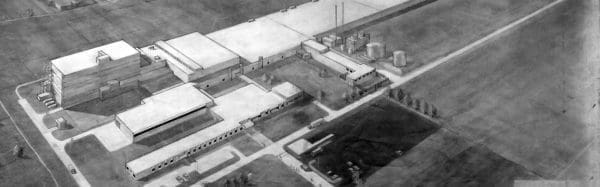
The American petrochemical multinational ESSO is developing the engineering project for the construction of a nylon production plant in the neighborhood of Santa Isabel, Zaragoza.
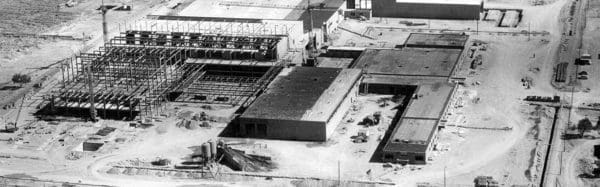
The construction and conditioning of the polymerization plant (P1) with four lines, the spinning plant (H1) with several sections, offices and service facilities is carried out.
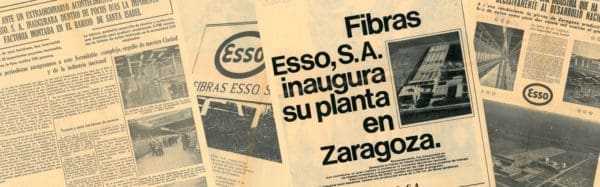
On December 10, production begins at the plant with 550 employees. In the following year, the official inauguration takes place, attended by the Ministers of Industry and Development Plan.
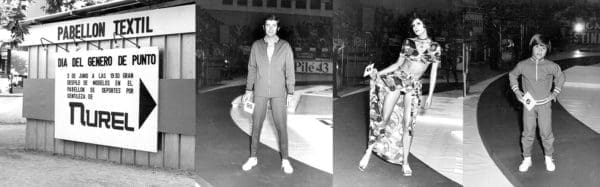
The ESSO Fibers nylon fabrics began to be advertised by means of model shows throughout Spain and by attending trade fairs. The trademark of the nylon fibers is NUREL.
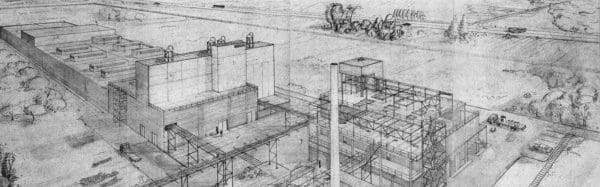
The plant is taken over by Banco Industrial del Mediterráneo and subsequently by the English company Imperial Chemical Industries. It is renamed after the brand name, NUREL, and the development of a new polyester production plant begins.

On January 25, the polyester yarn plant is inaugurated with the Minister of Industry. Daily production of 75 tons starts, under the polyester fiber trademark: TERYLENE.
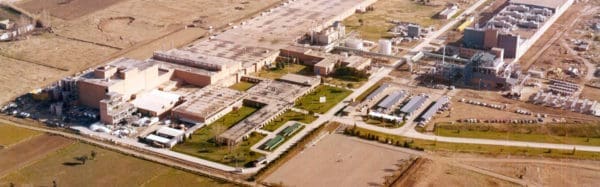
At the end of the decade, a caprolactam recovery and industrial waste depolymerization plant is started up for recycling. NUREL reaches its historical maximum number of employees, 1503.
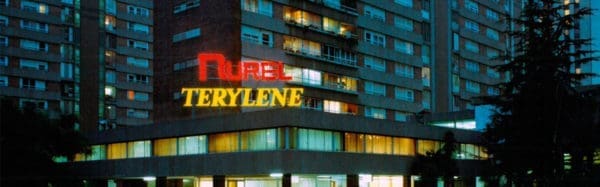
NUREL has its own logistic network, distribution warehouses and a central office in Barcelona where some of the most important departments are located.
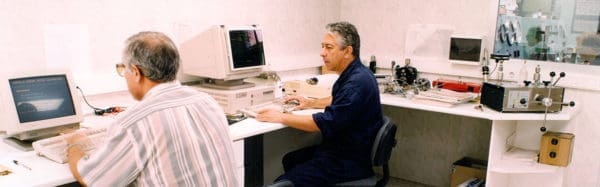
A cogeneration plant is inaugurated that converts, until 2005, primary energy into electrical energy and heat. The company starts working with PCs and an IBM-AS-400 management system with several terminals.
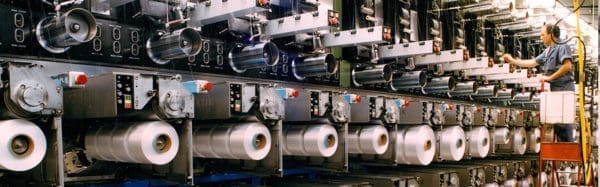
NUREL obtains ISO 9001 certification for quality management and assurance. A year later, the management team acquires the plant in view of ICI's intention to close it.
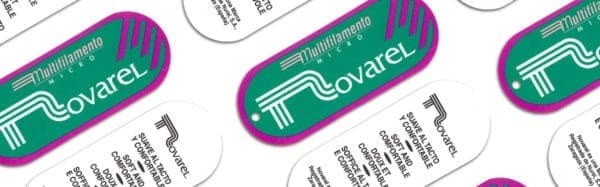
Production is changed from LOY to POY, the first warping unit is installed and new developments in polymerization begin. The multifilament yarn brand NOVAREL is launched.
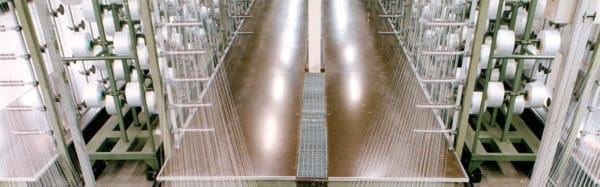
The Aragonese business group SAMCA purchases the NUREL production plant from the previous owner. In the summer of 1999, the first web site in the history of NUREL is launched.
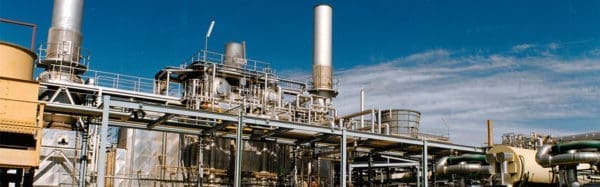
NUREL obtains the ISO 14001 certification for Environmental Management, which certifies the identification of environmental risks and the application of prevention procedures to avoid environmental accidents.
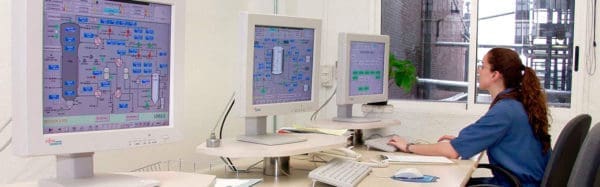
A new polyamide polymerization plant (P2), a new spinning plant (H2) and a mechanical recycling unit are started up. Production of microfibers begins.
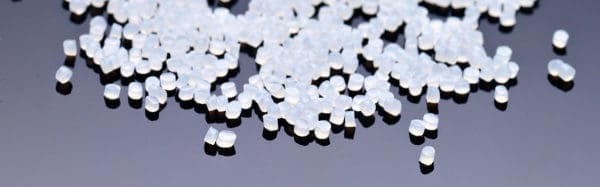
NUREL's plastic division is created since, up to that moment, all the polymer produced in the plant was used for self-supply. The following year the commercial brand NOVAMID is launched.
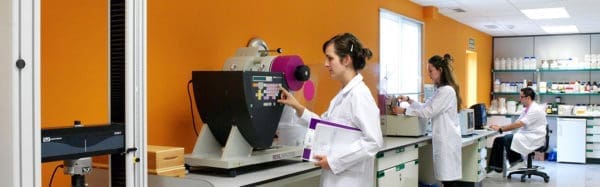
The first patent is published for the encapsulation technology used by NUREL, being the only company in the sector to produce cosmetic fibers. NUREL launches the range of cosmetotextiles with NOVAREL Aloe.
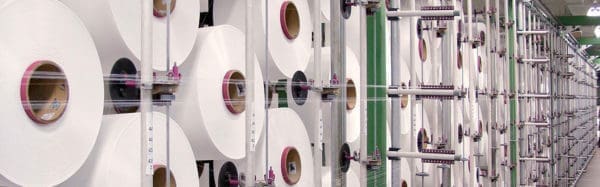
Some modifications are made in the plant to be able to produce new high viscosity recipes suitable for film, allowing NUREL to enter this market. The production of nylon 66 yarn in spinning begins.
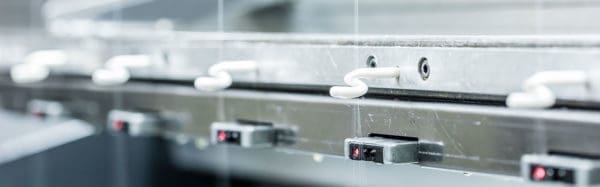
In January, a modern H3 nylon spinning plant is inaugurated, replacing the original 1968 plant (H1). A year later, the plastics division is relaunched with a new brand name: PROMYDE.
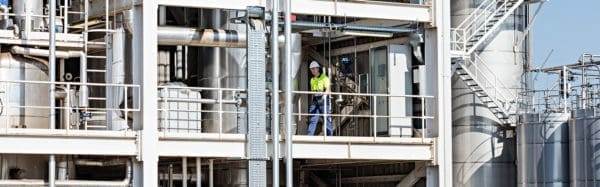
A Solid State Postcondensation unit is installed to produce high viscosity polyamide on a large scale, consolidating NUREL in the packaging and semi-finished products market.
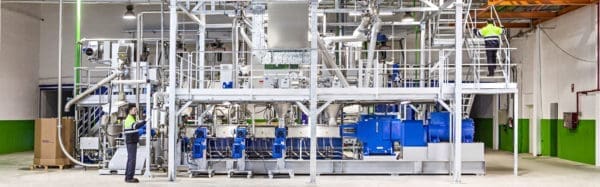
Opting for a more sustainable industrial development, the business is expanded with the start-up of a new biopolymers plant, INZEA. NUREL obtains ISO 50001 certification and the cosmetics sub-company ZEOMETIC is created.
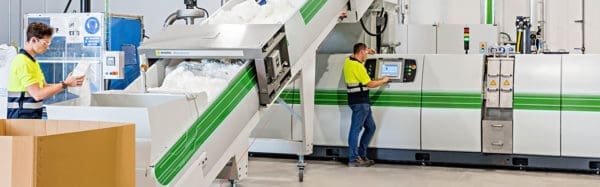
A new extrusion unit was installed to manufacture polyamide compounds and the re-grinding line was renewed to recover industrial waste and convert it into pellets suitable for production.
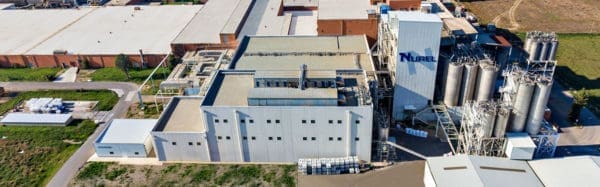
NUREL celebrates its 50th anniversary with 350 employees and produces 16,000 tons per year of compounds, 27,000 tons per year of polyamide polymer, 2,000 tons per year of recycled polymer and 7,200 tons per year of nylon filament yarn.
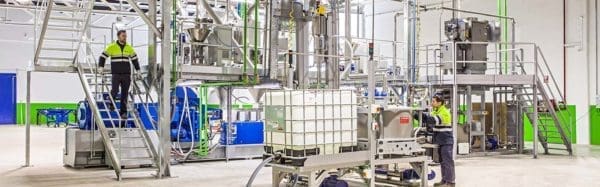
NUREL develops and introduces a new range of PBT and PET based compounds products, under the Terylene brand, expanding our markets in the automotive and electrical sectors.
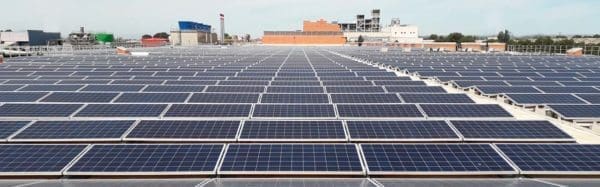
In line with the company's commitment to the environment, 22,568 solar panels were installed on the floor and roofs of NUREL's industrial area, making it one of the largest off-grid self-consumption facilities in Europe. Given the growing demand for more sustainable plastics, a second INZEA biopolymer extrusion line is commissioned.