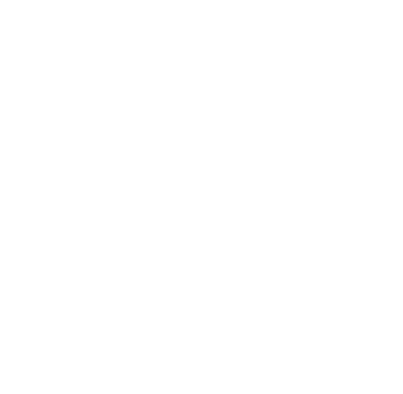
OUR PRODUCT LINE OF RECYCLED COMPOUNDS REDUCES THE ENVIRONMENTAL IMPACT
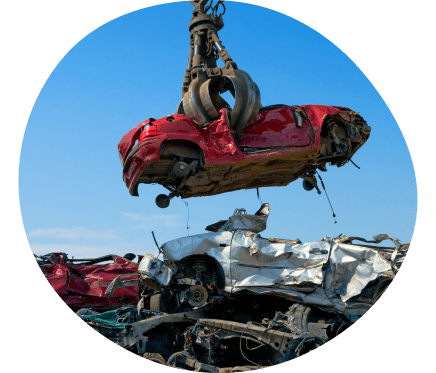
OUR RANGE OF RECO-LINE RECYCLED COMPOUNDS
Other sustainable solutions
100% RENEWABLE ENERGY → 30% FROM SELF PRODUCTION
28,310
Solar panels on 93,000 m 2
16,560 MWr
produced per year
11.85 MWp
Total installed capacity
10 MWh
Energy storage
INDEPENDENCE
From conventional electricity sources
10,991 t
Tons of CO2 saved
SECURED RECLAIMED MATERIAL FEEDSTOCK
EXTERNAL POST-CONSUMER WASTE VALORIZATION (PCR)
We are developing a collaborative network focused on automotive waste management, efficiently transforming end-of-life vehicle materials into high-quality PP compounds. This reduces reliance on virgin plastics and minimizes the industry’s environmental footprint.
In addition, through our UPtextile project, we transform discarded nylon textiles into engineered polyamides, supporting a circular economy. We also process recycled PET from packaging, expanding our portfolio of sustainable materials.

POST-INDUSTRIAL INTERNAL SOURCES (PIR)
NUREL is an integrated production site that includes polymerization plants, compounding units, recycling facilities and a complete nylon fiber spinning plant. We are committed to increasing productivity and reducing waste in all our processes by recycling all post-industrial waste generated.
Thanks to our state-of-the-art recycling units, we reconvert nylon waste into a range of consistent quality products with a reduced carbon footprint, fully aligning with our Zero Waste policy.

RECYCLED CONTENT CERTIFICATIONS

CERTIFIED RECYCLED TECHNICAL COMPOUNDS

EN15343 standard verifies the percentage of recycled plastic content used in the manufacture of any product.

ISCC PLUS is a mass balance certification that provides assurance about the sustainable content of a final product and ensures a robust traceability back to a sustainable source.

GRS (Global Recycled Standard) verifies the recycled material content throughout the supply chain, covering traceability, environmental principles, social responsibility, and labeling.
Our Recycling Process
1
We carefully source reclaimed materials from both internal and external sources. These materials then go through a rigorous identification and selection process at our facilities to ensure they meet the required quality standards.
2
These materials are remelted in our recycling units through a continuous mechanical recycling process.
3
The recovered polymers are stabilized and extruded in our compounding units, incorporating reinforcement additives, flame retardant agents, and colorants, ensuring that the final product meets specific performance, safety, and aesthetic requirements.
1. Post-industrial and post-consumer industrial waste
2. CONTINUOUS MECHANICAL PROCESS

3. RECYCLED POLYMER

4.COMPOUNDING

5. CERTIFIED RECYCLED CONTENT
POST-CONSUMER RECYCLED PP COMPOUNDS
CERTIFIED POST-CONSUMER RECYCLED CONTENT
Our Olexene®-Reco polypropylene (PP) compounds are derived from materials recovered from sources like automotive dismantling operations among other industrial waste.
The recycled content in these compounds is fully traceable and can be certified in accordance with EN15343 standards, ensuring transparency and sustainability throughout the production process.


Contributing to a more circular and sustainable future for the mobility industry
TRANSITION TO A CIRCULAR ECONOMY
The transition from a linear to a circular economy is one of the greatest challenges we face today. The European Union has set a clear objective: to decouple economic growth from the consumption of natural resources, aiming to achieve climate neutrality by 2050.
In particular, the European automotive market currently lacks sufficient integration of circularity in vehicle design and production, which results in a heavy reliance on primary raw materials. The quality of vehicle end-of-life treatment (ELV) is not yet optimal, leaving a significant unrealised potential for circularity in out-of-service vehicles.
The key areas of focus include circular design, enhanced recovery at the end of a vehicle’s life, and the incorporation of 25% post-consumer recycled plastic (PCR) by 2030. Of this 25%, a quarter must come from end-of-life vehicles, advancing a circularity strategy within the sector.
2030 AUTOMOTIVE INDUSTRY TARGET: 25% RECYCLED CONTENT
It is crucial to combat greenwashing with transparency, ensuring that this transition to a circular economy is supported by the necessary verifications that guarantee proper traceability throughout the value chain. This builds credibility with our customers and helps to clearly explain the environmental benefits of recycling. The use of certifications plays a key role in demonstrating our genuine commitment to sustainability.
OLEXENE RECO PP REDUCTION OF ENVIRONMENTAL IMPACT
CARBON FOOTPRINT COMPARISON
By choosing Olexene®-Reco for your automotive parts, you can significantly reduce their environmental impact and carbon footprint. Olexene Reco utilises post-consumer recycled material, eliminating the need for virgin petroleum-based resources. Additionally, the mechanical recycling process is carried out in our facilities, which are powered entirely by 100% renewable energy. This approach achieves notable reductions in carbon emissions, up to 78 % in 100% recycled products.


Up to 78% Carbon Footprint reduction.
OLEXENE-RECO PP RECYCLING PROCESS

NUREL partners with specialised companies to recover (PP) parts from end-of-life vehicles at dismantling facilities.

Our partners handle the shredding and sorting of PP, ensuring a pure, contaminant-free material for recycling.
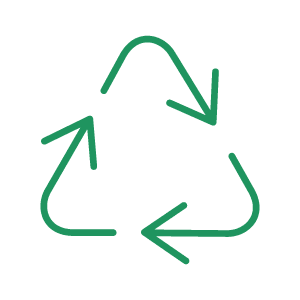
NUREL manages the entire reprocessing and compounding process in-house, transforming the recycled PP into high-performance compounds with reinforcements or FR agents.

The compounds are certified to ensure traceability, quality, and compliance with European recycling standards.

The certified recycled PP is used in the production of new automotive parts and other products, supporting a circular economy.
RECYCLED PA6 & PA66 COMPOUNDS
Recycling polyamide (PA) presents a significant challenge due to the limited availability of waste materials suitable for use in engineering plastics production. The scarcity of post-consumer PA waste makes it difficult to source high-quality recycled material.
However, thanks to NUREL’s vertical integration in the production of nylon synthetic fibres, we have access to top-quality pre-consumer material, ideal for manufacturing high-performance PA compounds.
Additionally, we have initiated the Up-Textile project, which focuses on repurposing waste generated during the textile manufacturing process, further enhancing the value and sustainability of our recycled polyamide solutions.
ONE SINGLE SITE, ONE SUSTAINABLE PROCESS
A key advantage of these recycled PA compounds is their low carbon footprint, as the raw material used is waste, and the recycling process takes place in the same facility where the waste material is selected.
This site also handles the mechanical recycling of the polymer and operates using 100% renewable energy.
Furthermore, the compounding process, where reinforcing agents and flame retardants are added, is conducted on-site, optimising efficiency and reducing the environmental impact.

RECOMYDE PA: DECREASING ENVIRONMENTAL IMPACT
REDUCING CO2 EMISSIONS BY 90%
The production of Recomyde® generates 90% less CO2 emisions than standard PA compounds. Therefore, a production of 1 ton of Recomyde reduces emissions of an equivalent to*:
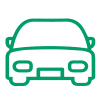
CO2 produced by a gasoline powered car driving 15,760 km

CO2 produced by 464,675 smartphones being charged

CO2 absorbed by 18,615 m2 of forest in one year

CO2 produced by 1.3 tons of waste recycled instead of landfilled
*Calculations based on Greenhouse Gas Equivalencies Calculator | US EPA
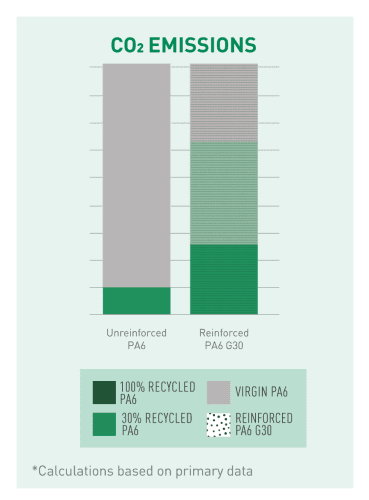
CERTIFIED RECYCLED CONTENT
All the recycled content in our Recomyde® PA6 & PA66 recycled compounds is certified in accordance with the EN15343 standard. Additionally, we offer certification options based on ISCC Plus mass balance or the Global Recycled Standard (GRS), as the waste material primarily originates from the textile industry.
These certifications ensure full traceability and transparency throughout the recycling process, guaranteeing the high quality and sustainability of our compounds.
PRE- AND POST-CONSUMER RECYCLING
NUREL operates an integrated production site with recycling facilities, where post-industrial waste from our nylon spinning plant is recycled into high-quality products, minimizing our carbon footprint and supporting the Zero Waste policy.
We also recycle discarded fabrics and nylon-based materials, such as fishing nets, films, ropes, and automotive parts, converting them into valuable engineering polyamides.
This initiative advances circularity and sustainability in the industry.
RECYCLED R-PET & PBT/R-PET COMPOUNDS
Proxylene-Reco R-PET reinforced with 30% glass fiber offers numerous advantages for injection-molded parts across various industries, particularly in the automotive sector.
This high-performance material combines the environmental benefits of recycling with enhanced mechanical properties, such as high strength, lightweight, chemical resistance and dimensional stability, making it an excellent alternative to traditional materials like virgin plastics or even metals.
NUREL offers custom formulations tailored to specific client needs, ensuring high performance and reduced environmental impact.


APLICATIONS
In the automotive sector, Proxylene-Reco R-PET 30% glass fiber reinforced is commonly used for engine covers, seat frames, dashboards, and various under-the-hood components. It also finds applications in electronics for protective housings, industrial machinery parts like gear housings and pumps, and durable consumer goods.
CERTIFIED SUSTAINABLE BENEFITS
Proxylene Reco is sourced from post-consumer PET packaging through SAMCA Group synergies, supporting circular economy efforts.
The recycled content of the product is certified according to the EN15343 standard, ensuring transparency and reliability in the use of recycled materials.
We provide Product Carbon Footprint for all grades (PCF).
Download our catalogues
Reco-line
Other technical recycled polymers solutions
Recyclable
Biobased and Biocircular
BIODEGRADABLE
Do you want to know all the news of Nurel Polymers?
Subscribe to the Newsletter